What is Porosity in Welding: Trick Elements and Their Impact on Weld High Quality
What is Porosity in Welding: Trick Elements and Their Impact on Weld High Quality
Blog Article
The Science Behind Porosity: A Comprehensive Guide for Welders and Fabricators
Understanding the elaborate mechanisms behind porosity in welding is important for welders and makers making every effort for impeccable craftsmanship. From the make-up of the base materials to the details of the welding process itself, a wide range of variables conspire to either exacerbate or relieve the existence of porosity.
Understanding Porosity in Welding
FIRST SENTENCE:
Assessment of porosity in welding exposes essential understandings into the stability and quality of the weld joint. Porosity, defined by the visibility of tooth cavities or gaps within the weld metal, is a common problem in welding processes. These voids, otherwise appropriately dealt with, can jeopardize the architectural stability and mechanical residential or commercial properties of the weld, causing potential failings in the ended up product.

To spot and evaluate porosity, non-destructive screening approaches such as ultrasonic testing or X-ray examination are usually employed. These methods permit the identification of interior issues without endangering the stability of the weld. By analyzing the dimension, form, and circulation of porosity within a weld, welders can make educated decisions to enhance their welding processes and attain sounder weld joints.

Aspects Affecting Porosity Formation
The incident of porosity in welding is affected by a myriad of variables, varying from gas shielding effectiveness to the ins and outs of welding specification settings. Welding criteria, including voltage, current, travel rate, and electrode kind, additionally impact porosity development. The welding method utilized, such as gas metal arc welding (GMAW) or shielded steel arc welding (SMAW), can affect porosity development due to variants in warm distribution and gas coverage - What is Porosity.
Effects of Porosity on Weld Quality
The presence of porosity also damages the weld's resistance to rust, as the entraped air or gases within the gaps can respond with the surrounding setting, leading to degradation over time. Additionally, porosity can impede the weld's capacity to hold up against pressure or influence, more endangering the overall high quality and dependability more information of the welded framework. In important applications such as aerospace, vehicle, or structural buildings, where safety and security and toughness are vital, the destructive impacts of porosity on weld quality can have extreme effects, stressing the relevance of decreasing porosity with proper welding methods and treatments.
Techniques to Reduce Porosity
Furthermore, making use of the ideal welding parameters, such as the right voltage, current, and travel speed, is essential in preventing porosity. Preserving a regular arc size and angle during welding also assists minimize the possibility of porosity.

Making use of the ideal welding method, such as back-stepping or utilizing a weaving movement, can likewise assist disperse heat uniformly and decrease the opportunities of porosity development. By carrying out these strategies, welders can successfully reduce porosity and produce premium bonded joints.
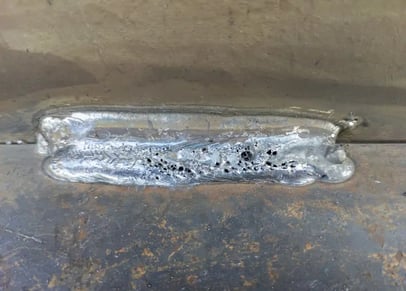
Advanced Solutions for Porosity Control
Implementing sophisticated technologies and cutting-edge methods plays a pivotal function in attaining exceptional control over porosity in welding processes. One sophisticated solution is making use of sophisticated gas mixtures. Securing gases like helium or a mixture of argon and hydrogen can have a peek at this website help in reducing porosity by supplying better arc security and improved gas protection. In addition, utilizing innovative welding techniques such as pulsed MIG welding or customized environment welding can likewise assist minimize porosity issues.
An additional innovative solution involves making use of sophisticated welding devices. Utilizing devices with built-in attributes like waveform control and advanced power sources can enhance weld top quality and lower porosity threats. Moreover, the application of automated welding systems with precise control over criteria can significantly minimize porosity problems.
Moreover, integrating innovative surveillance and evaluation technologies such as real-time X-ray imaging or automated ultrasonic testing can assist in discovering porosity early in continue reading this the welding procedure, enabling instant restorative actions. In general, integrating these sophisticated services can considerably improve porosity control and boost the total quality of bonded parts.
Final Thought
In verdict, comprehending the scientific research behind porosity in welding is vital for welders and fabricators to create high-grade welds - What is Porosity. Advanced solutions for porosity control can better improve the welding process and make certain a strong and reputable weld.
Report this page